Published: April 04, 2016 Updated: December 31, 2024
CMMS Primer
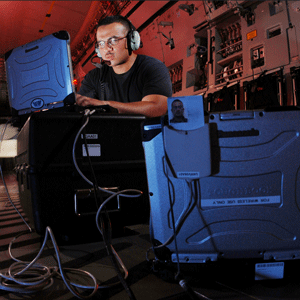
Across the nation, at facilities such as schools, hospitals, hotels, resorts and corporate campuses, industrial maintenance teams work hard to keep building and grounds infrastructure in top condition. As professional maintenance managers know, essential facilities maintenance tasks go way beyond custodial services. In fact, core-asset and equipment preventive maintenance, building repairs, remodeling and construction, groundskeeping, as well as, responsibility for operational sustainability efforts all normally fall to the facility maintenance department.
No wonder successful maintenance management deploy sophisticated CMMS software to assist them in these tasks! CMMS, or computerized maintenance management systems, can be used to track every piece of equipment, assign crews to tasks, and archive labor, inventory and other critical data.
Core CMMS Functionality
- Work Orders. At the very heart of any CMMS is the work order. By issuing a work order, the maintenance manager has selected a specific piece of equipment, identified a repairable problem, assigned appropriately skilled crew member(s), and authorized any necessary spare parts and tools from inventory. The work order is closed by assigned personnel when the repair is complete. A quality CMMS will reorder parts used and update the equipment record while billing appropriate departments (if applicable) and reporting labor and other cost data for use by other organizational departments (such as accounting and purchasing).
- Work Requests. A quality CMMS provides an easy procedure for authorized personnel to report requests for repair or down equipment to maintenance personnel. Maintenance managers can evaluate the request and dispatch a crew according to skill/trade and an assigned priority.
- Task Scheduling. Sophisticated maintenance management assumes a myriad of tasks must be undertaken over the course of the year. Normal preventive maintenance must be performed on almost every piece of equipment and the building infrastructure. Emergency repair events can occur at any time. A professional CMMS must contain a first-class scheduling capability that keeps skilled tradesman and other personnel efficiently assigned without inadvertently ignoring regular recurring work.
- Asset Status. A quality CMMS keeps track of every piece of equipment and asset over its useful life. Every item of equipment and every asset will be categorized by type and function and every specification, lock out tag out safety notice, and previous maintenance performed will be recorded. Major items of machinery or specialized infrastructure components may have a scheduled useful life that spans decades of use. Regardless, at some point, the costs of repair will outweigh the cost of replacement. This is where "gold-standard" CMMS really shines for the cost-conscious organization.
- Managing Inventory and Tools. Tool cribs, spare parts, and supplies such as expendable lubricants represent huge cost outlays for major facilities. Once again, a professional-quality CMMS, properly implemented, will identify waste and help management maintain lean inventory levels without jeopardizing productivity. With a top-notch CMMS, parts and tool availability will always be accurate and it will keep laser accurate maximum and minimum stock levels and reorder points. Finally, of course, expired or orphaned parts can be sold or removed.
In the 21st Century, CMMS is a software product
Today CMMS is, of course, best implemented using a software application. Depending upon the facility and the sophistication of its internal computer system(s), including personnel and IT security concerns, facilities generally opt for one of two basic CMMS solutions:
- A stand-alone CMMS software application purchased from a reliable CMMS software developer and installed on a facility-managed server; or,
- An SaaS (software-as-a-service) solution wherein the facility chooses a CMMS vendor to host the facility CMMS on the vendors servers and supply constant updates, security, data backups and support for the facility CMMS implementation.
A third, increasingly popular option may be CMMS for mobile devices. In this solution, maintenance staff equipped with personal or facility smartphones or tablets can carry the facility CMMS throughout the complex and so access the facility CMMS wherever they are, immediately.
It should be unsurprising to many that most of today"s high school and college-age youth are increasingly turning away from "traditional" personal computers and iMac laptops. Instead youth and young adults are transacting almost all their "business" directly on their mobile devices, usually Android or Apple smartphones or tablets. So Mobile CMMS is a natural technological progression for maintenance managers.
Why deploy a CMMS?
There are two fundamental advantages of employing a professional quality CMMS:
- The first is to realize significant cost savings by preventing unnecessary equipment failure and repair expenses by implementing a regular comprehensive preventive maintenance routine; and,
- Secondly, the facility protects, and even increases, its overall productivity. Higher equipment and asset "uptime" translates to optimum efficiency of both facility assets and personnel activity which, of course, translates to solid protection of the bottom-line.
There is little doubt that any well-managed facility, regardless of its mission, needs to deploy professional-quality CMMS. The only real question for serious maintenance managers to consider is whether your existing CMMS plan is doing the job well enough to accomplish your facility goals.