Published: December 06, 2024 Updated: December 31, 2024
Understanding Maintenance Expenses: How to Solve Expense Problems with CMMS
Businesses want to cut expenses. While you can achieve that goal, be sure the places where you're cutting don't come back to hit you with further expenses.
I'm referring to maintenance. Yes, you do put maintenance on the list of expenses. In this article, we'll explore that topic for better understanding.
Reactive Maintenance and Expense Problems
Many companies still operate under the mindset of not doing anything until something breaks down or fails. While there are advantages to this, in time, you risk more unplanned downtime. You might experience more emergencies, hurried purchases, and overtime on labor.
Preventative Maintenance: A Solution to Expense Tracking Issues
Preventive maintenance shows the proper way toward efficiency and lower costs. Routine inspections, cleanings, lubrications, and replacement parts are standard. You might conduct many of these during a planned shutdown.
PMs seek to reduce unplanned downtime. With a strategy to implement proactive measures, you'll see better production and extended asset life. In this and other areas, this means reduced expenses.
Discover how streamlined maintenance processes can elevate production. Learn more.
Breaking Down Maintenance Expenses for Better Tracking
The crux of this challenge lies in gaining deep insights into maintenance activities. You need to understand which actions and assets incur the highest costs and why. Therefore, you have to track maintenance costs at both the organizational and individual asset levels.
Maintenance costs encompass a spectrum of expenses incurred in preserving the optimal working condition of physical assets. The range of assets depends on the industry and company.
Vehicles. Property. Rental property. Processors. Conveyors. Storage units. Industrial ovens. Forklifts. And so many more. In addition, you have the regular system assets such as HVAC, plumbing, and lighting.
You use these metrics and reports to evaluate costs. These gauge the effectiveness of maintenance departments within these industries.
Hidden Maintenance Expenses and How to Solve Them
Neglecting proper maintenance has repercussions that extend beyond financial implications. It leads to increased labor, parts, and contract costs. Additionally, it results in:
- Lower product quality: You may have the equipment produce lower-quality products due to inadequate operation.
- Higher energy consumption: Assets that don't operate correctly tend to use more fuel, electricity, etc.
- Reduced asset lifespan: Review this discussion above. Neglected maintenance reduces the lifecycle of assets. PMs strive to keep assets at a baseline functionality, helping them to last longer.
- Extended downtime: Without proper maintenance, you'll see increased failures and downtime.
- Resource wastage: Reactive maintenance uses more inventory because of the continued failures.
- Environmental concerns: Improper or non-existing PMs may result in leaking fuels and chemicals.
- Safety risks: The biggie. Failures or breakdowns may risk employee injury or worse.
The above poses "hidden" costs to businesses. Most of the time, you see only the cost of the repair, labor, and inventory. You don't see expenses for maintenance neglect.
Overcoming Expense Problems with Strategic Maintenance Planning
A common misconception among business owners sees maintenance as a cost center. They don't relate that expense to producing a profit, an operational aspect that doesn't directly add to profits.
"I spent money on Asset A because it produces. I sell what it produces and earn a profit. Maintenance doesn't produce anything."
That's the mindset. Yes, the production side edges out maintenance in importance. Therefore, you discuss reducing maintenance.
Instead, look to maintenance as an investment. It keeps the assets functioning to produce a profitable product. In essence, this investment contributes positively to the bottom line in the long run.
Expense Tracking: Categories of Maintenance Costs
The article doesn't suggest that you spend willy-nilly on maintenance. Everything must work under a budget. To properly analyze that budget, review the categories of maintenance.
- Labor costs. A technician. A team. A crew. A craft. Who's available on what shift? How long does a worker take to complete a job? Do you have overtime? Do you have a delay in closing out a work order?
- Spare parts. Assets require inventory. Available inventory. Quantities must stay at a consistent level. Too much and you risk slow-moving parts. Too few means you might have to order an emergency shipment. and materials.
- Maintenance vendors. These consist of contracted professionals outside your company.
- Energy costs. Fuel costs for transportation to the job site. Electricity in-house.
- Overhead expenses. Offices. Stockrooms.
Your challenge comes when you have to properly track all of these expenses. Remember the mindset, that maintenance doesn't contribute to profit. Keep this in mind when collating data from the above expenses.
How CMMS Simplifies Expense Tracking and Management
Effectively tracking maintenance costs requires adopting advanced tools such as Computerized Maintenance Management Systems (CMMS). These systems streamline the measurement of costs by automated tracking. Technicians input data such as time spent and parts used, ensuring accurate data for analysis.
CMMS allows for the creation of detailed reports. These reports provide a comprehensive breakdown of costs for each of the aforementioned categories. A quality system also has those KPI reports.
Put together, you have a better view of where to make improvements in operations. Tracking assets and inventory. Labor attainment. Work order management. PM oversight.
Benefits of CMMS in Solving Maintenance Expense Problems
- Organization. You manage lists of assets, inventory, and PM activities. You have standardized work orders. You use the scheduling calendar.
- Less paperwork. You eliminate the cumbersome spreadsheets and handwritten work orders. Changes are less prone to human error.
- Reports. I've mentioned reports throughout this article. A quality system offers plenty of reports on all your operations.
- Information access. With a few clicks, you view information on any part of your maintenance department. With help from the CMMS provider, you can integrate your system with others. Information transfers to other departments for analysis.
The crux of controlling maintenance expenses lies in gaining a profound understanding of maintenance data. Knowing the actual costs incurred by assets provides a solid foundation for identifying areas to cut costs. As businesses navigate the complexities of maintenance management, having the right tools and insights becomes indispensable.
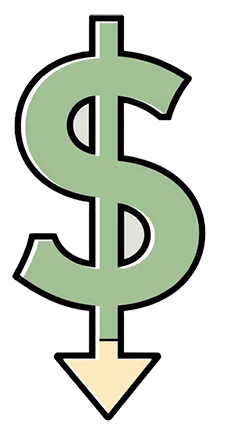
Reduce Maintenance Expenses with CMMS
- Plan what you need from a system. Discuss the modules and features that will benefit your company. Research and ask questions. You'll want to know about the following aspects of the system:
- Scalability. Will you get a lot of stuff in "package deals" you won't use? Or will you look for companies that offer pricing on what you want?
- Deployment. Do you want the company to host your system on the cloud, or do you have the necessary infrastructure to install on premise?
- Customization. Will the CMMS provider work with you for specialized reports and features?
- Implementation. Once you decide on a company, input the information into the system. You don't have to get too detailed at first. This will help with the transition into using the system.
- Training. Ask about training options. In-house, onsite, online.
- Use it. Start tracking:
- Asset readings.
- Inventory quantities.
- Expenses.
- Labor attainment.
- KPIs.
- Look for updates. Your business changes, so should your CMMS. Updates and improvements. New features and easier access.
Other CMMS benefits
Track equipment readings. Failure/Cause/Action codes.
Adopt inventory management systems to forecast inventory needs accurately.
Decrease spare parts inventory costs through streamlined management.
Improve training programs for machine operators to minimize equipment damage due to improper use.
Mobile capability for technicians in the field.
Track Vendor statistics - what are you buying from whom, how many at a time, what was the last price paid, etc.
Reports to stay compliant with regulators.
Streamline workflows to eliminate redundancies and over/under maintenance.
Predict potential issues before they escalate, avoiding expensive repairs and minimizing overall labor costs.
Emphasize preventive maintenance and predictive maintenance strategies.
Regularly scheduled maintenance reduces costs better than reactive repairs.
Of course, you'll need time to see the results. However, proper CMMS use can result in measurable improvements within ninety days.
Maintenance vs. Capital Expenses: Key Tracking Insights
Remember the above discussion where you consider maintenance an investment. While capital expenditures may fall into the same category, they have different aspects.
Regular maintenance costs include routine actions aimed at keeping assets in their original condition. Examples include: preventive maintenance, spare parts replacements, and simple repairs.
On the other hand, capital expenditures encompass more significant investments. For instance, major overhauls and upgrades substantially increase asset value. Capital expenditures go beyond routine maintenance. They contribute to enhancing the overall worth of assets.
One of the aspects of assets to track comes in the form of depreciation. This works to the benefit of both capital and maintenance. A CMMS can help track those values.
Reduce Maintenance Expenses with CMMS Solutions by Mapcon
While you have to consider maintenance an expense, you can control it. Businesses must leverage advanced tools like CMMS to gain insights. This involves understanding how much assets cost and why.
Look to Mapcon for CMMS software answers. Ask for a free demonstration of a superior system. Review the steps for proper CMMS usage and the aspect of a quality system.
Calling 800-922-4336 puts you in touch with U.S.-based trainers, programmers, and support. Start on the road to maintenance management success and reduce costs with MAPCON.
MAPCON CMMS software empowers you to plan and execute PM tasks flawlessly, thanks to its wealth of features and customizable options. Want to see it for yourself? Click the button below to get your FREE 30-day trial of MAPCON!
Try It FREE!